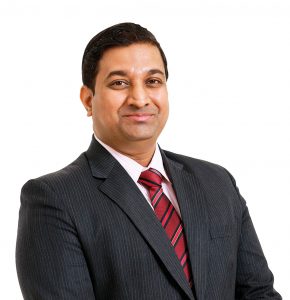
- INTELLICYIENT to help customers navigate convergence
New Delhi. 17 May 2021. “If a company operates in a regulated sector like Aerospace & Defense, or MedTech, there are additional challenges around regulatory compliances, facility approvals and audits, security and background checks, and the need to maintain a full record and traceability of every single part that goes into the end-product. There is also the after-sales segment that consists of spares, repairs, maintenance, etc. Today, most of these functions operate almost as silos often in a disjointed manner leading to enormous value leakage. With INTELLICYIENT, we help customers navigate the convergence of Information Technology (IT) and Operational Technology (OT) by closely aligning the information flow and the material flow through the product lifecycle,” Anand Parameswaran (SVP & Global Business Head, Cyient Digital) told Aviation & Defence Universe (ADU) in an exclusive interview.
ADU. Please explain the details of the solutions launched during the Hannover Messe
AP. Our core strength is working with companies that own, operate and derive significant value from physical assets. Some of these sectors include – Manufacturing (Aerospace, Rail, Automotive, Medical Devices), Utilities (Electric, Gas, Water), Communications and Industrial companies (Oil & Gas, Mining, Energy).
Combining our deep industry experience and strong Digital competencies, we recently launched INTELLICYIENT, a suite of Industry 4.0 solutions that will enable digital transformation for enterprises. INTELLICYIENT comprises of six solutions that cut across key industries supported by 9 technical studios:
- Connected Worker and Smart Factory: Enabling Industry 4.0 by integrating Industrial IoT (IIoT), cloud platform-as-a-service (PaaS), and industrial software for OT applications.
- After-Market and MRO Solutions: Developing digital solutions in the after-market services space to support maintenance and asset management processes.
- Intelligent Supply Chain: Enabling a digital supply chain experience throughout a product lifecycle to enhance planning and logistics functions.
- Location-Based Solutions (GIS Enabled): Developing digital solutions that drive process improvement focused on effective use of geospatial information in real-time.
- Digital Mobile Workforce Management: Empowering on-ground and offsite employees through digital tools that deliver a superior employee experience.
- Optimized Asset Management: Helping enterprises manage assets better by enabling them to visualize how they are used, and predict how and when they require replacement or maintenance using Artificial Intelligence and Predictive Analytics, IoT integrated data pipelines, edge computing and networking, and cloud native application architectures.
ADU. Enterprises implementing Industry 4.0 stand to create economic value of USD 3.7 Trillion by 2025. How does IntelliCyient’s range of digital solution make enterprises’ transition to Industry 4.0 more seamless?
AP. Industry 4.0 is primarily about integrating the flow of information and workflow within an enterprise. Having a clear foundation and understanding of how this information starts, flows from system to system, and gets transformed along the way is crucial to developing a clear and successful transition roadmap. If we take a typical product development lifecycle today, the process starts from a product specification based on user needs and market demand, it is then engineered, tested and manufactured on a shop floor. Then there is the inventory and supply chain management of raw materials and finished goods with quality control along the way.
We help our customers not just in solving the problem but in identifying the right problem to solve and prioritizing them in the context of their business.
ADU. What are the major themes that are rapidly transforming operations for Industry 4.0?
AP. We are currently experiencing a purple patch as far as technological advancements are concerned. From sensorization to cloud and connectivity, applications such as digital twins and digital threads, and integration of value chain systems like ERP, PLM, and MES with the supply chain, the technologies are continuing to evolve and mature.
The key catalyst to get all the cogs moving in sync is the ability to seamlessly connect the material, information and people connected to each other in real time. For example, most industries have a manufacturing BOM (bill of materials) and a separate engineering BOM despite both being for the same parts. While there are good reasons for these to exist, this kind of disjointedness, redundancy and duplicity makes it difficult for information to travel freely. This directly affects productivity and traceability of goods which results in tangible financial loss. The key is to get the entire enterprise on the same page, and the way to do it is by driving seamlessness through Industry 4.0.
Another major theme we are seeing is that the line between system functionalities are blurring between ERP systems, MES systems, PLM systems, etc. The advent of open source technologies, cloud infrastructure, private networks and new technologies in domain model connectivity and infrastructure as code are allowing very interesting disruptive forces to come in and accelerate the definition of time-to-value that is compelling for our customers
ADU. We have been talking about industry 4.0 from a very long time. However, companies still face challenges especially in the manufacturing and other legacy sector in implementing large scale digital solutions. How will IntelliCyient help enterprises transform in this hyper-digital new normal? What are the key priorities and focus verticals for Cyient?
AP. Digital is still in its early stages of evolution – it is not an exaggeration to say that we are at the Digital equivalent of where the Internet was with email and file transfers. While we see significant disruption already, it is fair to say that we are entering a phase where the disruptions will be much more significant in every aspect of business.
Use cases like predictive maintenance may have a wow factor today, but in 5 or 7 years, it will become commonplace like e-mail. However, the technologies are only as powerful as the people wielding them – our engineering DNA and domain expertise allows us to understand a problem and the business context to it allowing us to deploy the right technology in the context of the problem. In addition to the context, it also helps us accelerate the deployment of transformational solutions that also benefits our customers to keep pace with the dynamic environment of a hyper-digital world.
ADU. Are you planning to apply these solutions in the defence and aviation sector as well?
AP. Yes, Aerospace & Defense is a key area of focus for us, and we are looking to deploy solutions in this space. However, compared to other industries, Aerospace & Defense is behind the curve in digital adoption because it is highly safety critical and regulated. So the speed of change is always slower. That said, there is a huge demand post-Covid in the aviation sector for instance. The pandemic has forced the industry to shrink their operational footprint and as the market comes back up, it gives the opportunity to experiment and rethink the operations in fundamentally different ways.
In defense for example, there is a huge demand for location-based solutions and the ability to process data-on-the-fly-and-react has become mission critical. Similarly, intelligence collection and analysis not so long ago was a cumbersome process with collection, storage, secure transfer, access, processing and computing being different systems. This caused delays and inaccuracies in decision-making. Now we can help design systems that can collect a lot more data, do a lot more with the data, process it on the fly, and take action within minutes, not hours or days. This changes how missions are planned and executed.
In addition to this, like all manufacturing sectors, A&D will also see a bigger digital footprint and investment, the way factories are run, how MRO is done will all change within the decade.
ADU. Increasing resilience in manufacturing and automation seem to have become the need of the hour. How can the real-time data provided by INTELLICYIENT’s digital solutions help them in this?
AP. Resilience needs to be looked at both inside and outside your organization because all ecosystems and supply chains today are global. So, knowing what is going on around the world is as important as knowing what is going on in your factory.
For example, the semiconductor challenge has impacted every industry from hi-tech to industrial to automotive, because chips are everywhere. And the supply chain bottleneck is affecting everyone. So your ability to predict the risk in a supply chain due to a supply crunch or the financial health of your supplier or a broader technology change is critical. Knowing the points of failure in a supply chain and having real-time traceability helps scenario planning which can serve as an early warning system. This allows companies to hedge their risks and enhance their overall resilience.
Airplane OEMs can’t afford a plane worth $50 Million sitting unsold because a $100 part is unavailable. Our Intelligent supply chain solutions help avoid such scenarios by enabling real time and seamless-planning and execution of sourcing and procuring inputs throughout the product value chain and the manufacturing process. Our ability to architect and deliver intelligent supply chain and logistics solutions avoids such bottlenecks.
ADU. The pandemic has accelerated enterprises’ focus on Cloud and IoT. Building and managing IoT platforms and cloud-based applications to integrate systems has been the need of the hour. How does Cyient’s digital solution help enterprises seamlessly transition to the cloud
AP. Connected systems can be created without a cloud also. But doing it on a cloud makes development, deployment and maintenance a lot faster and convenient. Our core objective is to make sure processes are seamless, and see how data and workflows go through a system. Technology is just a medium, it is always evolving, and it will keep getting better. Today it is cloud, tomorrow it could be something else.
Another example is 5G – all the things that a private 5G network can do is mind-boggling. It is in the applications that a low-latency connectivity and a dense sensor connectivity can enable. So while technologies will keep improving, our focus should be identify and prioritize the right opportunities/problems to address.
ADU. What according to you is the future of Industry 4.0 and Automation in the Indian scenario?
AP. Indian manufacturing has been one of the earliest adopters of Industry 4.0. Given the abundance of technology talent and a buzzing ecosystem, a lot of companies are willing to try new technologies, so there is a definite appetite and a supportive ecosystem. However, the use cases in India will differ from a lot of other markets because the trade-off between people-cost and cost of automation is different. So, while an Australian manufacturing company needs automation because of its low population density, an American agriculture company may need automation and mechanization because of the large farms, and expensive labor, the business case in India will be driven by infrastructure challenges, lack of highly skilled labor etc. While the evolution of Industry 4.0 and the speed of adoption will be different, there is no doubt that Industry 4.0 will have a huge impact in India.
ADU. Any upcoming partnerships and developments that you would like to talk about
AP. Traditionally, OT implementations have had a relatively smaller footprint of partners compared to IT implementations. Digital, especially Industry 4.0 implementations depends on a robust, diverse and a highly collaborative partner ecosystem
While there are many players that need to come together, some of the key ones are the hyperscalers (AWS, Google cloud Azure etc.) who will play a big role. We expect to see ecosystems for specific industries coalescing around these platforms. Large OEMs that provide integrated platforms for Design, Simulation, Manufacturing, Quality Assurance, Supply Chain & Logistics will also be key players along with niche players developing highly differentiated industry-specific applications.
We see our role as an integrator that can collaborate with an ecosystem of partners to address the specific problems our clients are facing. Our role is to activate an ecosystem based on the needs of our clients and their industries.